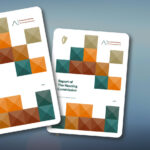
Where is the Report of The Housing Commission now?
1st July 2025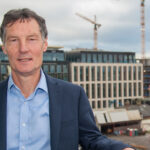
Marking 30 years of Clúid as we say farewell to CEO Brian O’Gorman
1st July 2025Innovative methods to scale residential construction
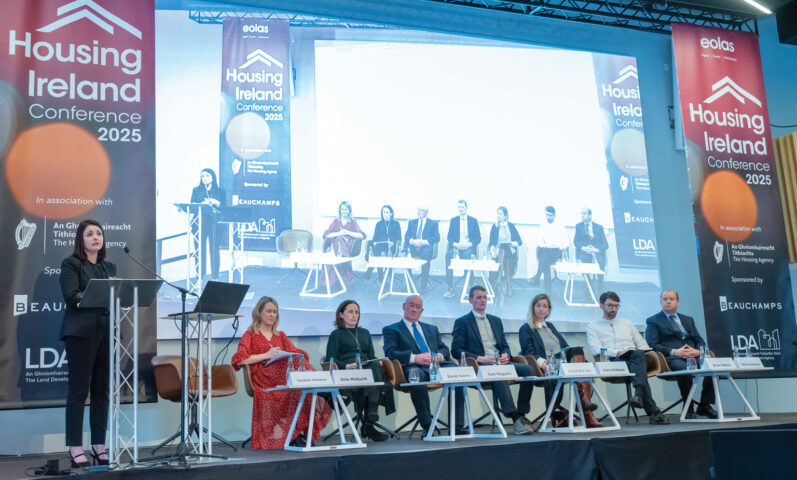
What are the remaining barriers to innovation in residential construction?
Orla McGuirk: One of the main barriers is existing regulations that limit the introduction of new technologies. Most technical guidance documents still do not fully account for modern methods of construction (MMC), and design certifiers typically follow these outdated documents.
Karen Kenny: We have changed housing and density standards to encourage innovation in design, but with MMC, you can still incorporate standardised elements. Raising awareness among planners is crucial so they understand why certain approaches are used and how they support MMC.
Tom Maguire: Understanding the full benefits of MMC is essential. On a direct cost basis, it may not always match traditional methods, but when you consider the entire lifecycle, it is more cost-effective. Market acceptance is another challenge. There is still some reluctance to adopt new systems, although this is improving.
Daniel McCrum: The construction sector tends to be project-focused, which limits long-term innovation. Certification is also a major barrier. Developing and approving a new product requires significant time and financial investment, which deters innovation.
Claire McManus: From a design perspective, the current standards can be overly restrictive. For example, in some cases, four dwellings require three staircases, which increases costs unnecessarily. Adjusting these requirements could allow for higher density and lower per square metre costs.
Brian Mallon: Certification is a major challenge. Although around 20 MMC systems now have Agrément certificates, there is still hesitation in accepting them, especially regarding fire safety. Even fully tested systems are often met with resistance. To advance, we need to embrace certified lightweight systems with better embodied carbon performance, and building control enforcement must become more consistent.
What is the key to unlocking the certification barrier?
Daniel McCrum: Building regulations must remain in place, but MMC – particularly volumetric systems – are relatively new and lack embedded codes and standards. Each new product has to be tested across all regulatory areas, especially structural and fire resistance. These tests are very expensive.
There are currently only 20 Agrément certificates, six of which are for insulated concrete formwork. The process of achieving certification through the MMC agreement pathway is resource-intensive and can take up to two years, which can deter companies from pursuing it.
Daniel McCrum: At Construct Innovate, we have testing facilities and research expertise from 11 research-performing organisations available to support the industry. These facilities are continually improving, but there is still progress to be made.
Claire McManus: As a practitioner, it often feels like the same steps must be repeated for every project. It would be helpful to reduce this repetition by publishing examples of newer typologies that have already passed fire safety or disability access certification. Knowing a typology has been approved on another site gives confidence in reusing it.
Orla McGuirk: Insurance or warranty products that provide cover for MMC would be beneficial. Training and upskilling the current workforce is also essential.
Daniel McCrum: A standardised design approach is being developed, starting with one MMC type. It will include construction details that are certified, compliant with building regulations, and published as supplementary guidance to existing technical documents. Making these resources openly accessible would reduce risk and lower the entry barrier for those adopting MMC.